|
|
Bioplastic
Recycling Infrastructure: PLA sorting
|
|
Sorting
PLA in recycling facilities is difficult
due to low volumes and in many cases,
the PLA container looks like PET. For
high volume recycling facilities, who
have installed the latest equipment, an
optical sort machine can scan and sort
PLA from PET or HDPE at high speeds (Biocor).
Watch
Video .....
|
|
Increase
of the bioplastic production in Germany |
|
BASF
has started operations at its expanded
plant for the production of the biodegradable
plastic Ecoflex®. Expansion of the
existing plant in Ludwigshafen (Germany)
will increase production capacity for
Ecoflex from 14,000 to 74,000 metric tons
per year. At the same time, BASF will
ramp up compounding capacity for Ecovio®,
a derivative of Ecoflex.
“We are already successful in the
market with our biodegradable polyester
Ecoflex and the related innovation, Ecovio.
The larger production capacities will
enhance our position significantly,”
said Dr. Wolfgang Hapke, president of
BASF’s Performance Polymers division.
“The capacity expansion will also
enable us to respond even more effectively
to our customers’ wishes.”
Ecoflex is a plastic that has the properties
of conventional polyethylene but is fully
biodegradable under industrial composting
conditions in accordance with DIN EN 13432.
Read more .....
|
Notes
from Bioplastic Reshaping Industry
conference – Las Vegas February
2011 |
|
Nike
– the apparel & shoe maker gave
an interesting view on their approach
to sustainability. The key interest is
to use bioplastics to reduce the carbon
footprint, on the basis of proven LCA
advantages. Very interesting is also to
see how Nike prioritizes it’s effort.
1. Identify where the main impact is ?
materials / manufacturing (not use, logistics
or end of life…)
2. In materials, what are the primary
material streams in apparel it’s
polyester & cotton, in footwear it’s
rubber & EVA
3. start working on reducing tox, carbon
footprint, waste and water on each.
In parallel to that Nike is working on
closing the loop and setting up recycling
schemes, f.ex. using recycled PET from
bottles for sportswear.
The Bio-PET race is on !
Coca-Cola presented it’s PlantBottle
The key reason why Coca-Cola care about
packaging is that it’s the most
important driver for increasing sales
of beverages. Coca Cola are working on
making PET bio based by making the two
main PET components (ethylene glycol and
terephthalic acid) bio-based. The first
step was to use bio-based ethylene glycol
.
Read
more .....
|
|
A
future generation of biodegradable
Polyester compounds |
|
BASF
Corporation announced that it has
received a license from Metabolix
under U.S. Patent No. 5,883,199, titled
“Polylactic Acid-Based Blends,”
to produce and market PLA (PolyLactic
Acid) and PBAT (PolyButylene Adipate co-Terephthalate)
compounds under the BASF trade name Ecovio®.
Ecovio biodegradable polymer is a blend
of Ecoflex® biodegradable aliphatic-aromatic
copolyester (PBAT) and polylactic acid
on the basis of corn. The University of
Massachusetts is the owner of the ‘199
patent, and Metabolix, Inc. is its exclusive
licensee in the relevant field. Metabolix,
Inc. is a leader in the use of bioscience
to provide biobased, sustainable, solutions
for the world’s needs for plastics,
fuels and chemicals.
Ecovio can be used to extrude biodegradable
films without any further admixtures or
preparation and is used to create tailor-made
blends to meet customer needs.
Source
.....
|
|
Introductions
of bioplastics reached a crescendo
during 2010 – A point of view! |
|
....Introductions
of bioplastic materials and products reached
a crescendo during 2010, as more mainstream
companies introduced bioplastics from
a dizzying array of commodities. Beverage
maker Odwalla, a Coca-Cola subsidiary,
said it was switching all of its single-serve
drinks to bottles made almost entirely
of plastic derived from molasses and sugarcane
juice. (In 2009, Coke announced it would
begin phasing in a similar bioplastic
bottle for its flagship cola.)
Procter & Gamble is bringing sugarcane
to shampoo and makeup with new packaging
that will be on shelves next year. The
company will start using sugarcane-based
plastic packaging for certain products
from its Pantene Pro-V, Covergirl and
Max Factor brands, made with ethanol derived
from Brazilian sugarcane.
Sugarcane is just the start. Electronics
company NEC said it developed a bioplastic
made with an extract from non-edible cashew
nut shells and plant cellulose that is
twice as strong as another bioplastic
typically made from corn starch.
Source
.....
|
|
Heinz
Adopts The PlantBottle! |
|
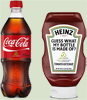 |
Starting
this summer, Heinz ketchup will
be appearing in plant-based bottles
developed by Coke. The Coca-Cola
Company and H.J. Heinz yesterday
announced a partnership under which
Heinz will start using Coke’s
PlantBottle packaging for all 20-ounce
ketchup containers. The PET bottles
are made partially from Brazilian
sugarcane ethanol and have a lower
reliance on non-renewable resources
than traditional PET bottles, Coke
said. Up to 30 percent of PlantBottles
comes from plants, and the bottles
are fully recyclable. |
There’s no difference between the
PlantBottle and Coke’s old plastic
bottles in shelf
life, weight or appearance, according
to Coca-Cola vice president of environment
and water resources Jeff Seabright.
Heinz said its adoption of PlantBottle
technology would be the biggest change
to its ketchup bottles since the company
introduced plastic containers in 1983.
It said the packaging switch is an important
step in its plan to reduce greenhouse
gas emissions, solid waste, water consumption
and energy usage by at least 20 percent
by 2015.
Read
more .....
|
|
How
is biobased PET manufactured? |
|
PlantBottle PET plastic beverage bottles
are made with up to 30 percent of their
PET material derived from plants. The
Coca-Cola Company has worked with partners
to develop a process for making PET plastic
bottles that contain a blend of traditional
material and up to 30 percent plant-based
material. The plant-based material is
made from sugar cane and molasses, a by-product
of sugar cane processing.
In some markets, its used both recycled
content as well as plant-based material
in the PlantBottle packaging. For bottles
that use recycled material, the recycled
content plus plant-based material should
enhance the environmental benefit associated
with PlantBottle packaging by further
reducing the use of virgin petroleum-based
material during manufacturing.
A PlantBottle PET bottle feels like traditional
PET plastic, it’s the same weight
as traditional PET plastic, it works just
like traditional PET plastic, and it’s
recyclable just like traditional PET plastic
— because it is PET plastic.
Read
more .....
|
|
PHAs
market in packaging is still extremely
small – A point of view! |
|
PHAs
are linear polyesters naturally produced
by bacterial fermentation of sugar or
lipids. Telles,
the US-based bioplastics joint venture
between renewable chemical company Metabolix
and agribusiness firm Archer
Daniels Midland (ADM) is ramping up
the world’s largest commercial-scale
PHA plant in Clinton, Iowa, US, designed
to produce 110m lb/year (50,000 tonnes/year)
of the corn-based plastic under the brand
Mirel.
Telles began making commercial shipments
ofMirel PHA to customers when it started
the facility in March 2010, according
to Metabolix CEO Rick Eno. The company
anticipated the plant running at full
capacity by mid-2013.
“We expect a number of new customer
announcements for Mirel as we continue
to establish the foundation for this substantial
business,” says Eno. “Mirel
is now commercially available in a variety
of grades including thermoforming, injection
molding, cast/blown film and sheet. It
can replace many petroleum-based plastic
materials from olefins and styrenics to
ABS [acrylonitrile-butadiene -styrene]
and polycarbonate [PC].”
Read
more .....
|
|
Sugar
as alternative to petroleum |
|
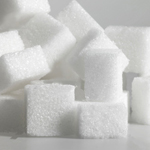 |
A
major product is bioplastic such
as bio-polyethylene made from
sugarcane-based ethylene. Brazilian
chemical company Braskem
is a prominent developer in this
area. Braskem also recently announced
its development partnership with
enzyme company Novozymes for bio-propylene
using sugar-cane as feedstock.
Also in Brazil, sugarcane and
ethanol producer Pedra
Agroindustrial plans to start
commercial bioplastics production
by late 2012 using sugarcane-based
poly-3-hydroxybutyrate (PHB).
Meanwhile, European chemical company
Solvay
is also developing bio-polyvinyl
chloride (PVC) using sugarcane-based
ethylene. |
Read
more ..... |
|
|